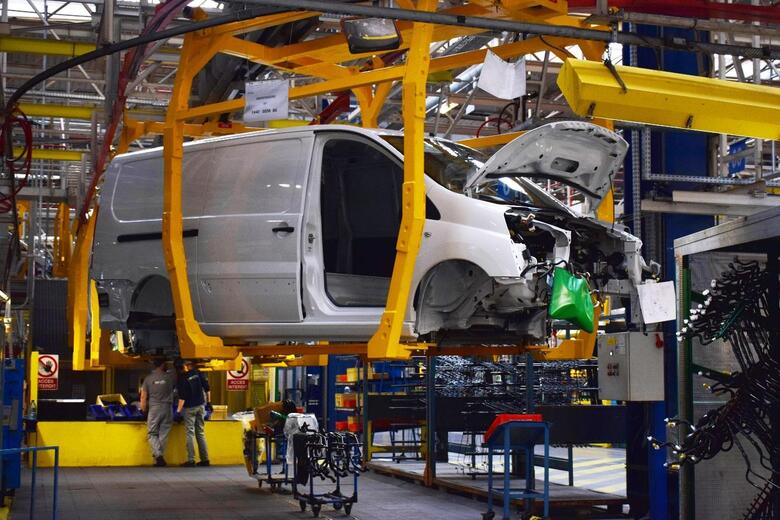
Manufacturing is central to the operational efficiency of the supply chain. Traditionally, manufacturers produced by forecasting demand for their products. However, surplus stock and higher inventories are a burden for a manufacturing business. With the arrival of Lean manufacturing, firms started producing goods as and when they were needed. This industry continues to achieve higher manufacturing efficiency to offset the rising costs of business.
Table of Contents
What is Lean manufacturing?
This system uses a procedure that maximizes productivity while reducing waste. The system views waste as something that does not add value and that customers would not want to buy. This is called Lean production, a method that is based on particular manufacturing concepts that have impacted production worldwide. Lean manufacturing includes reduced lead times, ongoing expenses, and enhanced quality of goods.
The main aim of Lean manufacturing is to eradicate waste and constantly refine a process. This sustainability gives customer value. The waste consists of products, services, operations, and activities that require money, time, and skill but do not generate customer value. These include excess inventories, underused talent, and wasteful or ineffective processes. Removing inefficiencies should mean services run more smoothly and costs are reduced.
Lean manufacturing is about making problems visible so they can be addressed and solved. Smart technologies can enhance and accelerate the ability to implement Lean manufacturing and drive improvement. Lean is the methodology of problem-solving, and innovative technologies can support this because it makes information more readily available. Lean removes waste, while technology ensures speed in removing waste, enabling a solution to be reached more quickly.
Kettering University offers a Lean manufacturing master’s degree with the addition of a Master of Business Administration. Earning both degrees takes two years and demonstrates the leadership, organizational skills, and personal discipline necessary for success.
Toyota and Lean manufacturing
The Japanese car maker Toyota has a vehicle production system that has become well-known throughout the world. The Toyota Production System (TPS) is based on eliminating waste and utilizing the most efficient methods. Toyota’s vehicle production system is a way of making things by a Lean manufacturing system or a Just-in-Time (JIT) system and has come to be renowned and examined worldwide.
The TPS detailed the types of waste that do not give value to the customer. These wastes were:
- Waiting — either people or idle equipment.
- Over-production of a product.
- Over-processing of a product.
- Unnecessary transportation.
- Excess inventory.
- Excessive movement of people, machinery or equipment.
- Faults that require costly correction.
The TPS was based on continuous improvement over many years, focusing on daily decisions, operations, and goals. The aim was to make vehicles as quickly and efficiently as possible. The TPS was established using Jidoka (a Japanese word meaning automation with a human touch), which resulted in equipment closing down straightaway if a problem occurred, stopping faulty products from being produced. The system also used the Just-in-Time concept, meaning each process only produced what was needed for the next step. The result was vehicles that were made quickly and fully met customer requirements.
The system entailed constructing and improving systems until they were safe and reliable. Engineers built each part manually to exacting standards, then consistently simplified the operations. Human skills and technology were combined to achieve maximum efficiency and accuracy.
To fulfill orders, the vehicle is built efficiently and as soon as possible by adhering to these steps:
- When the order is received, production instructions must reach the start of the production line without delay.
- The assembly line must have all the necessary parts in stock to assemble any ordered vehicle.
- Parts that have been used on the assembly line must be restocked using the preceding process.
- The preceding process must have all types of parts in stock and produce only the number of parts that the operator has used.
The TPS is based on eliminating waste to achieve the most efficient methods. It has evolved through years of research and development — even today, Toyota continues to improve this system.
Lean manufacturing versus traditional manufacturing
Traditional manufacturing is related to mass production. Manufacturing products on a large scale and keeping surplus stock is the basis of traditional manufacturing. This principle stems from the economies of scale idea, where businesses produce products using non-unique technologies.
The purpose of traditional manufacturing has been to make large numbers of similar or identical products based on sales forecasts, without understanding the customers’ needs.
Traditional manufacturing is a production method that has been used for a long time. It is a process of using labor, tools, and machines to produce goods. There is a strong focus on mass production, intending to produce considerable numbers of products efficiently and cost-effectively. Traditional manufacturing typically uses a linear production model where every part of the process is fixed and in a logical sequence. The end product is made one step at a time rather than through continuous improvement. The same process is repeated until the correct number of products has been made.
This traditional system maximizes output at all costs, meaning that safety and quality can be overlooked. To maintain efficiency, capital investment is needed to buy new tools and machinery. The production process can be inefficient because of a need for more new and original ideas. Traditional manufacturing can produce more waste, which means more cost and concerns about the environmental impact.
One of the main differences between Lean and traditional manufacturing is the view of resources.
Traditional manufacturing regards resources as expenses, but Lean manufacturing sees resources as an asset that can be used to give value to the customer. Lean manufacturing works to reduce waste and make the most of resources, while traditional manufacturing can overlook inefficiency and waste money and time.
Another contrast is the speed of production. Lean manufacturing has short production cycles to give value to customers quickly, while traditional manufacturing has a longer production process. Traditional manufacturing swiftly produces large quantities of products, but it takes longer to get them to market.
Lean manufacturing emphasizes customer feedback and quality control, while traditional manufacturing has typically been less concerned with these elements. Lean manufacturers use customer feedback to make their processes better continually, but traditional manufacturers may not address customer feedback at all. Traditional thinking sees mass production as essential to a successful product. In contrast, modern thinking sees flexibility and efficiency as more important than quantity in production.
Lean manufacturing and traditional manufacturing have their own advantages and disadvantages. Lean manufacturing gives operational efficiency, reduced costs, improved product quality, increased speed and decreased inventory. However, traditional manufacturing focuses more on meeting customer demand by having products readily available in big enough quantities. It is also more labor intensive, so it can produce large numbers of products quickly. If a company needs to increase production quickly, traditional manufacturing may be most suitable.
Why is Lean manufacturing important?
Waste in the industry can include inactive workers, inefficient processes, and unutilized materials, and are detrimental to productivity. Lean manufacturing works to remove these. The reasons for doing this can range from providing customers benefits to increased profits. The following are the main benefits of Lean manufacturing:
- Eliminate waste: waste is an adverse factor for resources, deadlines, and cost. It contributes no value to services or products.
- Improve quality: enhanced quality lets companies remain competitive and meet customer needs.
- Reduce costs: excess materials can incur storage costs but can be reduced with better processes and materials management.
- Reduce time: inefficient working practices can waste money, while efficient methods mean decreased lead times and services and goods being delivered more quickly.
These are the main principles of Lean manufacturing:
- Value: this depends on how much customers will pay for services or products. This value is generated by the business, which works to eradicate waste and reduce expenses to get the best cost for the customer while also making a profit.
- Map the value stream: this involves analyzing the resources and other materials needed to produce a service or product to recognize improvements and waste. The value stream addresses the whole journey of a product, from beginning to end. The production cycle should be investigated, and anything without value should be withdrawn. Current manufacturing is often complicated, requiring the shared work of many people including designers, scientists, and engineers.
- Create flow: this is about removing barriers and having better lead times. Flow production involves the continuous movement of items through the production process. When one task is completed, the next task must start immediately. Disorganized production processes create costs, and the aim is for processes to operate smoothly with little hold-up or waste.
- Establish a pull system: this strategy only works when the demand is there and requires communication, efficient processes, and flexibility to perform successfully. Products are only made to meet customer demand. All the company’s resources are used for producing goods that are sold straightaway.
- Perfection: the quest for perfection comes through the continual improvement of processes. Lean manufacturing demands constant assessment and improvement of procedures to eradicate waste, and to find the best system for giving customer value. An organization’s culture should have continuous improvement ingrained and should require measuring production cycles, lead times, cumulative flow, and throughput. Every staff member in the company should recognize the importance of continuous improvement.
Muda, Mura, and Muri
Acknowledging the three types of inefficiency help to avoid wasted materials, time, products, and human effort. Muda, Mura, and Muri are types of waste that are harmful to productivity, workflow, and customer satisfaction. They are Japanese terms that can support Lean manufacturing and provide guidelines for avoiding wasteful use of resources.
Muda means wastefulness. Work that has no value is split into two parts: work that is necessary but not recognized by customers as adding value, and work that is not necessary. The first kind of Muda could be safety testing and inspection, which do not directly add value to the final product but are essential to ensure a product is safe for customers. The second type of Muda includes activities with no value that do not benefit the customer and, therefore, should be discontinued. There are seven divisions of waste in this type of Muda: transport, inventory, motion, waiting, over-processing, overproduction, and defects.
Mura means irregularity and is seen to cause the seven wastes under Muda. During production, goods go through numerous workstations throughout the assembly procedure. When the scope of one workstation exceeds the others, you will see a collection of waste in the form of waiting and overproduction. A Lean processing system aims to have an even workload so that there is no waste collection or unevenness but the delivery of the correct number of products at the right time.
Muri means overworked. Excessive workloads can be caused by Mura or by excess removal of Muda. When people or equipment are overworked, they are more likely to fail. Machines can break down, and there can be employee absenteeism and illness, reducing productivity. Fair work distribution can help avert Muri and not overload any equipment or employees.
Real-world problems are dynamic, and the needs of customers are constantly changing, meaning work processes must also change. When standardizing work and designing processes, the impacts of Muda, Mura, and Muri can be considered, and production strategy can be optimized to develop a Lean manufacturing system.
Conclusion
Lean manufacturing is a production method that can help improve and streamline processes to enhance customer benefits while saving time and money by eliminating waste. The Lean method is best applied across an organization with continual monitoring and improvements being applied with the support of all employees. Toyota has demonstrated how successful this system can be and has attracted interest around the world. There are benefits and drawbacks to both Lean and traditional manufacturing, but currently, many organizations are turning to Lean manufacturing.
Leave a Reply